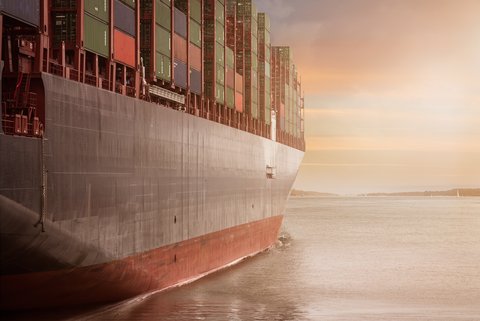
Going with the flow
Acounts payable processing and reading invoices with JobRouter®
It only took two months for the largest Bavarian inland navigation company, MSG, to start process incoming invoices electronically. Since the beginning of 2015, the JobRouter® digital process automation platform has been on board as part of the regular routine of the accounting department and has transformed invoice handling into a lean process. This has also helped them to take advantage of early payment discounts.
No tears
No tears were shed by Kerstin Brück for the good old days of manual booking stamps and account sheets. The IT administrator and accountant is a big JobRouter® fan. Everything changed in late October of 2014. Together with a project team made up of department heads and a JobRouter partner, Brück developed a test configuration in only four days. "I thought we would have more problems. But almost immediately during the test we got that feeling - 'It works!' The result was nearly a 100 percent fit." A two week trial run confirmed that feeling.
Advantages
Incoming invoice processing with JobRouter®
- Ideal for a central automated incoming invoice recognition and matching
- Processes data from email invoices and scanned invoices
- Reads header data automatically - Date, invoice number, sum, tax, currency
- Integrates creditor recognition: reads supplier master data and provides it in forms
- Allows indexing, tagging and archiving together with JobArchive
Project details
- Client
- MSG
- Industry
- Inland Waterways Navigation
- Employees
- 82
- Instances
- 150 instances / day
- Database
- MS SQL
- Ongoing processes
- Electronic invoice reception, electronic archive /// Modules: JobStart, JobMind Head, JobArchive,
- Planned processes
- /// Integration: SAGE ERP software, ISS industry software /// Project duration: 2 months, from JobRouter® test to the productive process //// database MS SQL
Getting to the bottom of the procedure
That the two-week trial in early November was such a success can be attributed to the good preparation of the shipping specialists. Brück"s project team compiled a detailed assessment that included; departments and categories, flows for incoming or outgoing receipts, responsibilities, validation rules, and interfaces to the ERP system and dispatching software. First and foremost, the familiar mail folders were mapped electronically. This ensured that invoices from the main business, inland navigation, and from the secondary dockyard business and bunker operations reach the right departments.
The members have highest priority
As a cooperative organization, MSG wanted to ensure that members' invoices received prioity. The cooperative provides freight contracts and planning security to its members. It also simplifies their life on the water by collecting, booking and paying their invoices and providing them with a monthly statement. Based on the earlier preparations, MSG was able to get the JobRouter test up and running quickly. The entire process - from receiving the invoice to verification that they are factual and amounts are correct to final review - was automated.
I am a total JobRouter® fan!
I work with both accounting and IT, therefore I was already delighted during the test configuration. Now that I see how simple and structured everything runs, I can only recommend JobRouter®. Participating in developing the process was fun. It allowed me to do a lot myself, create fields and I can intervene at any time. The JobRouter® digital process automation platform is self-explanatory. Colleagues from all departments gave me positive feedback. My advice: Give it a try! I cannot think of a reason that speaks against it.
![]()
Kerstin Brück
IT administrator
MSG eG
New at the helm: Header data recognition of JobMind Head
Brück was surprised that not every department was in need of a separate workflow. After the first day, it was clear that there was a "framework that looks reasonable". Compared to a ship's sonar, the electronic locating of documents is quite simple: A barcode is put on every invoice before it is processed by a scanner connected to the local network. The barcode activates the JobMind Head module that then automatically reads the header data of the invoice and ships the recognized data to a JobRouter® process.
The invoice number, date, sums and taxes of more than 95% of the German-language invoices are recognized, centrally stored in the system and can be processed with booking forms. For invoices from the Netherlands or Belgium, around 80% of the header data is recognized correctly. JobRouter® pulls the matching vendor data from accounting and displays the payment agreement as well.
Cast off to the final configuration
During the first test, users were brought on board, questions were answered and suggestions made. The archiving of all documents was a success right from the start. JobRouter® transports all data and documents to the end of the line, the harbor called JobArchive, where they are stored and are audit-proof. At the end of November, the processes were set to their final course. Access authorization groups were established in JobArchive. This allows every group to have their own digital storage space and unauthorized access is blocked. In-house invoice numbers are now used electronically as internal coordinates for navigation and to search and filter. A separate info area was created for the management of the cooperative.
Within two months everything is running on schedule
With JobRouter® on board, early payment discounts are now used regularly. "In the past, it was problematic when time was lost on the mailing route between the dockyard and headquarters," remembers Brück. That stress is now gone. Data from the existing source systems, that generate the expected incoming invoices during freight transactions, are now imported into the dispatching software through JobRouter®. After being processed, JobRouter® retrieves the records and delivers them to accounting.
Praise for a super workflow
"I like working like that," praises Kerstin Brück. To make it easier for colleagues, fields were labelled with familiar terms. She designed user training focused on activities and complemented by hardcopies. The keyword search is a popular process as well. Another advantage is the history log, also known as an audit trail. The audit trail keeps track of all process activity and records when steps were processed and by whom. An audit trail PDF is attached to the archiving log.
"It is insane what the interface of JobRouter® provides," appreciates the IT administrator. The JobRouter system is linked to our ERP system and matches the goods receipts to the invoices such as fuel for the bunker or materials for the dockyard. The sum per goods receipt and what was processed is also displayed. "Transparency is much higher and we have significantly more control. If we receive a call or have to verify a reminder, we can see the status of an invoice at any time or retrieve the data instantly from the archive. You just have everything you need," she summarizes.
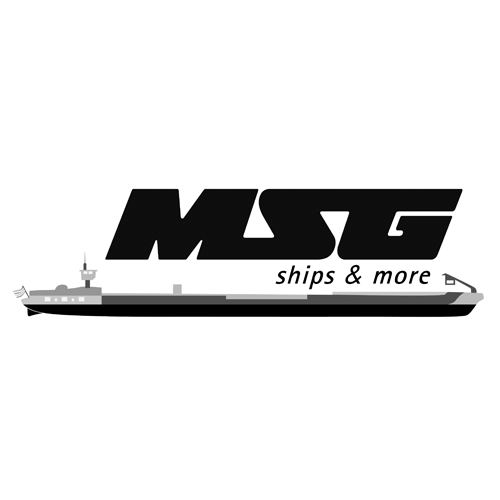
Short profile - MSG
The Main Shipping Cooperative – MSG - is the largest inland shipping company in Bavaria. Since its founding in 1916, the headquarters of the transport company are located in Würzburg, Germany. A fleet of more than 70 inland waterway vessels is formed from the ships of its members (independently owned) and MSG owned ships. MSG specializes in the transport of dry cargo (e.g. iron ore, heavy goods, animal feed) on the European waterways of the Rhine, Main and Danube including many subsidiary waterways. The shipping routes include Germany, the Netherlands, Belgium, France, Switzerland, Austria, Slovakia and Hungary. MSG maintains its own dockyard in the city of Dorfprozelten on the Main River in Bavaria. Their service portfolio also includes warehousing and transhipment services, freight brokerage and bunker services.. Bunker services are the supply of the necessary operating materials, technical equipment, refueling and consumer goods to the ships and their crews. Stationary refueling of ships occurs at the bunker station in Würzburg and en-route refueling is handled by company-owned bunker boats. Multiple subsidiaries and associated companies are part of the shipping and port handling sector between Rotterdam and Vienna.