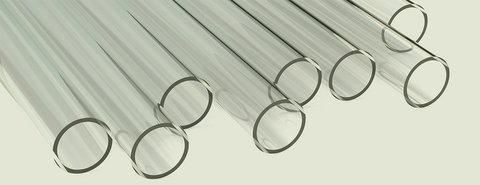
Workplace of the Future
IBM Notes replaced by Microsoft and the JobRouter® Digital Process Automation Platform
Schott Tubing, a business unit of specialty glass manufacturer Schott, has replaced their previous IBM Notes environment with the Microsoft suite. For the migration of databases and for business process workflows, Schott Tubing now relies on the independent JobRouter digital process automation platform.
Migrating manual processes to digital platform
In the Bavarian glass-town of Mitterteich, Germany, glass has been melted and processed since the 19th century. The main location of Schott’s Glass Tubing business can be found here. Schott Tubing makes glass tubes, rods and profiles from more than sixty special glass types for applications in the fields of pharmaceutics, industrial and environmental technology, and electronics. As a part of a project called “Workplace of the Future” the company’s IT group decided to take their IBM Notes infrastructure out of service and to migrate applications to the Microsoft platform. The switch to Exchange Server and Outlook met their expectations, though it was difficult to find a quickly applicable solution to handle their approval processes and databases, which had been manually programmed in Notes.
After a JobRouter presentation performed by their long-term IT partner ProComp Professional Computer, the Tubing business unit decided to do a field test of two different solutions: the Nintex SharePoint extension and the JobRouter digitization platform.
Advantages
Benefits of the JobRouter platform replacing IBM Notes
- enables the replacement of even complex Notes infrastructures
- integrates the e-mail client of Microsoft Outlook into processes in an uncomplicated way
- easily links processes and triggers e.g. approvals controlled by e-mail according to the business rules in process steps
- graphical process designer reduces manual programming work
- simplifies form-driven processes with subtables
- a system-independent digitization platform that offers higher performance
- through extremely high ease-of-use, flexibility and customization
- modularly expandable and easy to scale
- self-explanatory: extremely little training needed
Project details
- Client
- Schott Tubing
- Industry
- Manufacturer of special glass for glass tubes, glass rods and profiles
- Employees
- 2,000 worldwide
- Ongoing processes
- Price list releases, bonus releases, credit notes, sample dispatch, modification process for serial production, internal purchasing instances, travel expense handling, certification verification, authorization request
- Planned processes
- Optimization/expansion of existing processes, introduction of digital process automation to other business unit//// Instances: about 350 per year //// Integrations: Microsoft SQL Server, individual software Tubing Price Master, Microsoft Exchange
The Challenge
JobRouter® versus Nintex®
Markus Frauenreuther, Director Business Services & Solutions, is responsible for the IT environment at Schott Tubing. “One of our main criteria was that we wanted to design and manage the processes ourselves.” So he sent two of his employees to the beginner courses of both suppliers, to enable them to create two standard processes on their own; their travel request and request for new IT hardware. The difference was immediately apparent, especially during the modification of processes. “We realized quickly that we could work more easily with the JobRouter platform. It is self-explanatory and less complex – two clicks and the process is modified”, Markus Frauenreuther summarizes.
The following requirements were set for the new software:
- investment-security, independent from the product life cycle
- system-independent Stand-Alone solution
- usability and controllability for the IT department and the users
- open system architecture for the connection of upstream systems and subsystems, independent from the product life cycle
- transparent cost structure with regard to purchase and ongoing support
We came quickly to the understanding that JobRouter® covers all our requirements.
![]()
Markus Frauenreuther
Director Business Services & Solutions, IT
Schott AG
Next steps - Creating processes themselves
Multi-Stage processes in the test environment
The next step was the handling of more complex workflows with multi-stage and parallelized releases in the JobRouter test environment, installed by ProComp and then transferred into the productive system upon completion.
The support of a Notes developer was needed with the old system. Now the internal team was able to create new processes themselves for the first time using the JobRouter process designer. At first, the focus was to convert paper-based processes into digital ones – for example the authorization of factory tours. Also, approvals that have been managed for years by routing e-mail chains through departments were quickly translated into a JobRouter process and redesigned from scratch, if necessary.
“We achieved successes quickly and raised acceptance for the JobRouter digital process automation platform by digitizing complicated and time-intensive operations first”, Markus Frauenreuther states. New employees no longer need several weeks to find their way around complex organizational operations. They become productive much faster.
These changes are especially appreciated by employees who are Digital Natives. They expect their employer Schott to be equipped with the latest technology. Also, the workplace of the future is site-independent and mobile. That’s why the international divisions of Schott are linked via VPN and approvals can be authorized via e-mail through mobile devices – JobRouter handles them all in the same way as direct entries.
JobRouter is THE platform for work processes. Whenever I have a process, which involves several employees, releases, and information obligations, JobRouter plays an important role.
![]()
Markus Frauenreuther
Director Business Services & Solutions, IT
Schott AG
A mailbox for raw material certificates
According to Markus Frauenreuther, the role JobRouter plays is about increasing “quality, speed, and transparency” in processes. This can be shown best by the example of the automated control process for raw material certificates. Consignment notes, which were previously passed on via many paths from the incoming goods department to the laboratory and the quality department, are now collected in the form of scans or files in a special digital mailbox monitored by JobRouter.
JobRouter automatically starts a workflow as soon as a new document arrives. On average, JobRouter reports four to five times a day in parallel to the three departments that a new certificate must be checked. As soon as the system receives approval confirmation from all the departments, the document is automatically indexed by keywords and stored in an audit-proof way.
Streamlining change management
New modification process with a moment of revelation
So far, the most comprehensive new workflow is a 4-M process. If, for example, a measuring tool in production needs to be changed, a GMP-compliant modification process is necessary (Good Manufacturing Practice). The impacts of the modification have to be investigated and evaluated, and safeguards have to be defined and scheduled. Finally, the results have to be documented. This core process of operational risk management ensures that the company is in compliance with DIN EN ISO 9001. The former procedure was based on a paper control document, which was time-consuming and costly to fill out and which was sent or carried manually from decision-maker to decision-maker.
Today an online JobRouter process named “modification request for serial production” replaces the old manual process. The new process guides all persons involved through the complex procedure quickly and easily. Everything is clear and self-explanatory. Employees no longer need to spend time researching how to make an application, how the processes work, or who is involved. The implementation of the process through the Schott team was supported by ProComp. All required information – such as technical drawings, sketches, or photographs – are attached and provide a unified basis for decision making by all persons involved in the process.
“Like all agile development, we had numerous iteration steps and gained a taste for it, as the saying goes”, Markus Frauenreuther summarizes. “We noticed the great flexibility JobRouter offers. And we decided to involve even more staff in the 4-M process. The system makes it easy for the user, taking them by the hand and leading them through the process.”
Interview
- Mr. Frauenreuther, why did you decide on the JobRouter digitization platform?
Within the scope of our “Workplace of the Future” project our aim was to make the way we work and the technology we use more sustainable. In JobRouter we found a Stand-Alone solution, which makes us independent and which can be linked to any sub system and side systems, thanks to the open system architecture. Two employees are sufficient to supervise and enhance the platform adequately.
- What are the main benefits for you?
For me these are the speed, flexibility, and control. A two-step approval process does not take more than 3-4 days to develop – no comparison to the previous procedure.
- Which projects do you plan for the future?
With our positive experiences and successful projects our colleagues from other sites are listening with open ears to our suggestions. With the support of ProComp we are about to connect more business units to the platform.
Automating more processes
Samples, price lists, overviews, multiple languages
Now even tasks, for which there was no completely standardized process before, can be managed by JobRouter. One example of this is the production of samples. There is no item in the ERP system for small glass tubes, which our clients need as product samples. Today, a simple JobRouter process collects all required information from the sales and product engineering departments and forwards the request to the product planning department. This has cut the lead time for samples in half, to only two days.
Price list management is another example. A custom process developed by Schott itself is linked to the JobRouter digitization platform. As soon as a price modification is saved in the subsystem, JobRouter updates and delivers the value according to the predefined business rules. The platform is also useful for inventory and data hygiene activities in user management, creating an overview on access rights and authorizations to connected interfaces.
Transactions in sales and distribution processing, including rebate applications, bonus requests and complaints are also managed with JobRouter. “We are constantly working on new processes,”, Markus Frauenreuther says“. The next step will be to examine the use of a Portuguese JobRouter solution for our site in Brazil. Our colleagues from Schott Electronic Packaging in Southern Germany, also expressed strong interest in the introduction of JobRouter.”
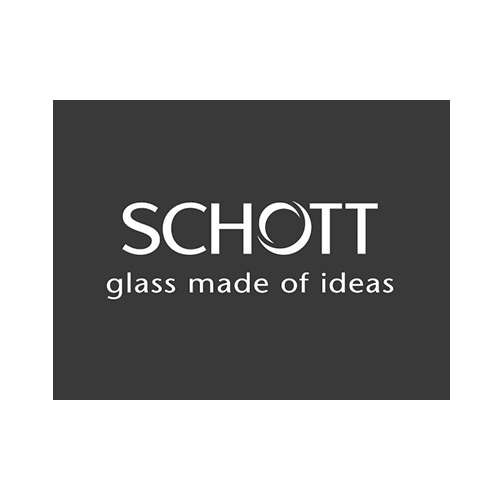
Short profile - Schott / Schott Tubing
SCHOTT is one of the world‘s leading technology corporations for special glass and glass ceramics, with production and distribution sites in 34 countries. The subsidiary Schott Tubing, a leading glass tube producer, is headquartered in Mitterteich, Germany with facilities in Europe, Asia and South America. The company makes glass tubes, rods and profiles from more than sixty special glass types with a production capacity of more than 140,000 tons. SCHOTT offers tailor-made products and services for international growth markets such as pharmaceuticals, industrial and environmental technology and electronics. Globally, more than 15,000 employees work for the SCHOTT, with about 1,200 at the Schott Tubing site in Mitterteich.