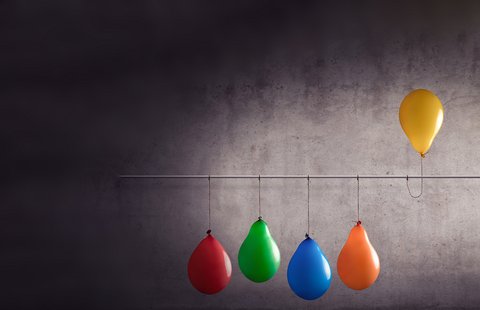
Methods used to improve your processes
Process optimization - successfully increasing efficiency
- Last updated
- Reading time
- Category Process automation insights
Examples of process optimization methods include Total Quality Management, Lean Management, Kaizen, and Six Sigma. You can find out more below about what lies behind these concepts and how process optimization methods work. You will also find examples of how companies can optimize their business processes with special software.
Simple explanation
What is process optimization?
Process optimization is defined as a systematic procedure for improving business processes. In specific terms this means that: You don't need to rethink your company as the processes are already in place. The key is simply to optimize the processes in order to be more economically successful. There are different ways of doing this, which we will present to you later on.
What are the aims of process optimization?
The main aims of process improvement are:
- to increase the efficiency and effectiveness of existing business processes and
- to optimize the use of resources.
Companies generally want to secure or improve their competitive position at national and international level.
In concrete terms, this means that companies improve their processes in order to reduce costs, minimize throughput times, reduce other expenses, improve quality, or perfect capacity utilization. Other possible aims of process optimization include improving communication (internal and external) and making changes in relation to sustainability. The potential is individual and extends across all areas of the company from production and sales to HR and accounting.
The first question to address is which business processes need to be optimized and in what order. Every company should spend sufficient time taking a close, critical look at itself to determine the major or most decisive levers.
How does process optimization differ from process management?
Process optimization or business process optimization is part of process management and the BPM life cycle. It is a continuous process rather than a completed task, as shown in the diagram. The other phases apart from business process optimization are analysis, modeling, execution, and monitoring. The whole process can therefore be divided into five steps.
In addition: Companies use process digitalization and process automation to improve processes with the help of software and digital tools.
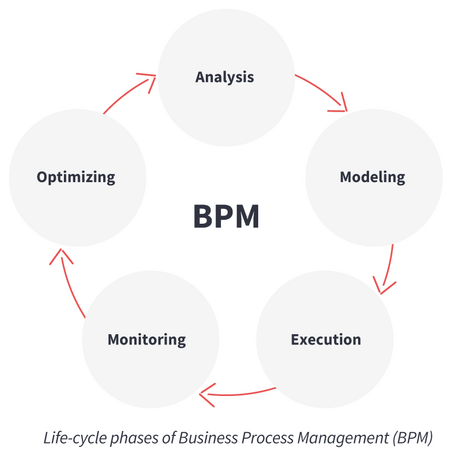
How does process optimization differ from process management?
Process optimization or business process optimization is part of process management and the BPM life cycle. It is a continuous process rather than a completed task, as shown in the diagram. The other phases apart from business process optimization are analysis, modeling, execution, and monitoring. The whole process can therefore be divided into five steps.
In addition: Companies use process digitalization and process automation to improve processes with the help of software and digital tools.
Choosing the right approach
What kind of process optimization methods exist?
Processes can be optimized using different methods. The type of company and the area to be optimized determine which is the right method to use. The most popular methods are presented below.
1. Business Process Reengineering (BPR)
Business Process Reengineering (BPR) involves reorganizing the business processes. The emphasis is on significantly improving business processes in terms of key figures such as costs, quality, service, and throughout times. In contrast to other process optimization methods, it does not focus on individual processes, but is more concerned with having a positive influence on the fundamental structure of all the internal corporate processes.
Four key statements need to be taken into account in process optimization with BPR:
- The main focus is on the decisive business processes.
- Customer requirements are at the heart of all processes.
- The company focuses on its most important skills.
- Information technologies provide great support for business processes.
These four statements are underpinned by the four “Rs” of reengineering:
- Renewing: This phase involves integrating and training employees more effectively in organizational terms.
- Revitalizing: The second phase involves redesigning the process. The processes are optimized in this phase.
- Reframing: In the third step, it is important for everyone in the company to let go of old thought patterns and to experience the improved processes.
- Restructuring: Finally, the portfolio of activities has to be improved.
2. Total Quality Management (TQM)
Total Quality Management (TQM) is equivalent to all-encompassing quality management. The focus is on the customer, as the aim of TQM is to improve customer satisfaction through process optimization and in doing so remain competitive.
The following statements are central to TQM:
- Customers: Quality is geared to customers.
- Employees: Quality is achieved by employees.
- Dimensions: Quality consists of many dimensions.
- Process: Quality is not the aim but a continuous process.
- Products: and services: Quality relates to the processes required for production.
- Action: Quality derives from deliberate action and needs to be developed.
3. Lean Management
The lean management method focuses on time and resources, or more specifically, how to optimize them and utilize their capacity. The aim: To minimize waste and optimize customer benefits. In a narrower sense, process optimization through lean management reduces waiting times, streamlines workflows, and optimizes costs. The underlying philosophy: Every step in the value chain should be efficient and ultimately provide customers with the best possible benefits. In addition to quality, the company's flexibility is also put to the test in this process.
Lean management raises the following fundamental questions:
- What is the value of the product from the customer's point of view?
- How long does the overall value creation process take for a product?
- How long do individual value creation processes take?
- Which departments and teams are involved?
- How can we create a value chain without interruptions or waiting times (also relates to warehousing)?
- How and where can we avoid errors?
- How do we continually keep up with processes and respond flexibly to our customers’ behavior?
- How to we involve employees and improve team work?
The principles of lean management:
- Value: Determining customer value
- Value Stream: Analyzing the value chain
- Flow: Creating and maintaining a value-added flow
- Pull: Responding to customer requirements
- Perfection: Keeping a constant eye on the process with the aim of perfecting it in the long term
4. Kaizen
Kaizen is a process optimization method that originates from Japan, and more specifically from manufacturing technology. The term encompasses the idea of continuously striving to improve everything and constantly incorporating innovations. “Kai” means change and transformation and “Zen” means improvement.
The prerequisite for Kaizen is that employees and the organization must always question themselves with a critical eye. This means that: Everyone works on the assumption that the potential for improvement is inexhaustible. Kaizen is therefore more of a mental attitude or a philosophy than a method.
The five pillars of Kaizen include:
- Process orientation: The emphasis is on process optimization rather than results.
- Customer orientation: The customer is always right. Specific features: In Kaizen, employees are also considered as customers and as such are highly esteemed. This attitude allows all employees to develop a positive relationship with the company and its activities, which helps to improve internal processes.
- Quality orientation: Companies that operate in the spirit of Kaizen set themselves high quality standards, which they check regularly using key figures and measurements.
- Criticism orientation: Criticism is not negative in Kaizen, but rather an opportunity for improvement. Criticism is welcome. Employees can make suggestions for optimization, which are thoroughly examined and incorporated if the results are positive. This creates an almost endless process of reflection and improvement.
- Standardization: An implemented innovation is also considered a new standard; ultimately it has already undergone a critical quality check. Once standardization is complete, it is critically scrutinized again, and the process starts again from the beginning.
Different methods can be used within Kaizen to achieve the goal of endless improvement and process optimization.
- 3 “Mus” (Muda, Mura, Muri): avoiding waste, imbalance, and overload
- 5 “Ss” (Seiri, Seiton, Seiso, Seiketsu, Shitsuke): remove anything unnecessary, sort out what is left, keep your space clean, keep going, make the 5 Ss a habit
- TQM (Total Quality Management): check and document all processes with regard to quality
5. Six Sigma
Six Sigma is process optimization based on figures and statistics. Six Sigma is based on the assumption that every process can be represented mathematically. This explains the name “Six Sigma”: Sigma stands for the standard deviation of a population, i.e. a deviation from the mean. If the value is too high, it indicates that the process is inadequate. This is where Six Sigma comes in. The method determines the cause-effect relationship. It highlights the causes of problems and therefore points out any weak spots. Six Sigma is not only concerned with quality optimization. The method can be used to improve all processes.
Six Sigma is carried out using the DMAIC cycle: Define, Measure, Analyze, Improve, and Control. It is based on the following five questions:
- Define: What is the problem, which key figures can be used to represent its scope, and what is the goal to be achieved?
- Measure: Which steps in the process are responsible for this? Measuring and calculating process performance.
- Analyze: What are the main causes of the problem highlighted by the data?
- Improve: How can the problem be solved through optimization?
- Control: How does the organization ensure that process optimization is maintained long term (and does not simply come to nothing)?
Companies have been implementing successful process optimization for some years now by combining Six Sigma with lean management. Time and costs are put to the test in this context as well as quality.
Practical use
Examples of process optimization
One example of process optimization is the improvement of HR processes based on the following elements:
- Digital holiday request
- Digital personnel files
- Digital travel expense reports
- Digital employee onboarding
- Digital business trip request
Improving processes and digitalizing HR increase employee satisfaction and work transparency, while ensuring that information is exchanged seamlessly.
Achieving your goals with the right tools
Which software is suitable for business process optimization?
Process optimization software is called a BPM tool (Business Process Management Tool). The tool helps you not only to improve business processes, it also supports you in modeling, implementing, and automating them.
These solutions enable you to consider your processes holistically, make better use of resources, minimize errors, save time, and ultimately increase efficiency. You can find out more below about how to do this with the JobRouter® digitalization platform.
Start optimizing your processes now
How JobRouter® can support your business process optimization
The JobRouter® digitalization platform helps you to make better use of resources and increase efficiency. You can use the flexible, customizable solution in numerous application scenarios from invoice processing to contract management.
How can we make your processes better? We digitalize and automate your workflows, network processes, data, and documents throughout the company and work alongside you to move a step closer towards digitalizing your company. Find out more about our functions and request a Demo.